The Deep Drive update we were all waiting for š here it is again in case you missed it over on Kickstarter...
Anatomy Of The Multi DriveĀ

Chuck
Letās start at the business end of Multi Drive, the simple and elegant chuck. This piece is machined from a solid billet and has been thinned down to reduce as much weight as possible. Thanks to an internal fine thread, when turned the cone on the end closes down against the internal collet and closes it up, providing the needed clamping force to hold in the bits. The shape in the internal end is a very tricky geometry, thatās not the easiest to get to and has to be really precisely machined to achieve the clamping force we require.
When we were making the early prototypes, we ground up a custom boring bar to get inside and machine the angle in. All the machining is done before a hardening process, that changes the crystalline structure of the metal to make it much harder. So hard, that Itās no longer machinable we use an induction hardening where most hardening processes just put a hard coating on the outside layer of metal, ours penetrates all the way through to the centre.
This gives our parts a unique strength and toughness not normally used outside of specialist engineering applications, in the chuck it means that we can have a thin light weight steel that is incredibly strong and hard wearing. So, there you have it, now you know something about metallurgy!
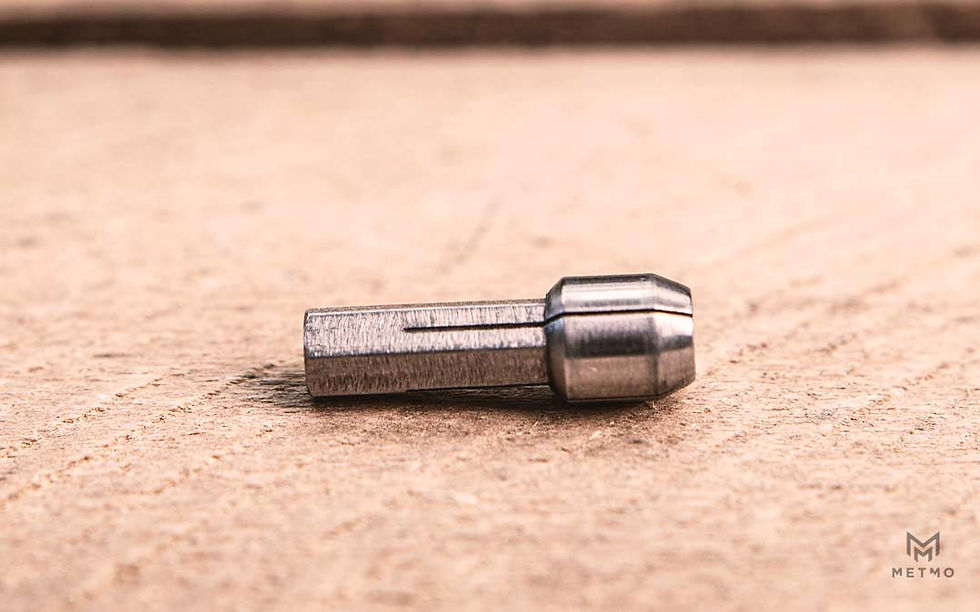
Collet
Inside the chuck sits our humble collet, a custom designed hexagon shank gives it a firm engagement. Unlike a normal collet that would only spin in one direction this shape means that it can withstand a twisting motion of a screwdriver and the uneven pressure in different directions.
Made of a special type of stainless spring steel, once heat treated this metal goes from very rigid to a much more spring like material, we are using a very thick section of it here so itās not like a conventional spring that will be all bouncy, but instead will last a lifetime of repeated flexes and powerful clamping šŖ.Ā
The fine thread inside the Chuck allows a large mechanical advantage to be applied to the end of the collet and the shallow pitch of the thread locks everything in place with no slack at all.
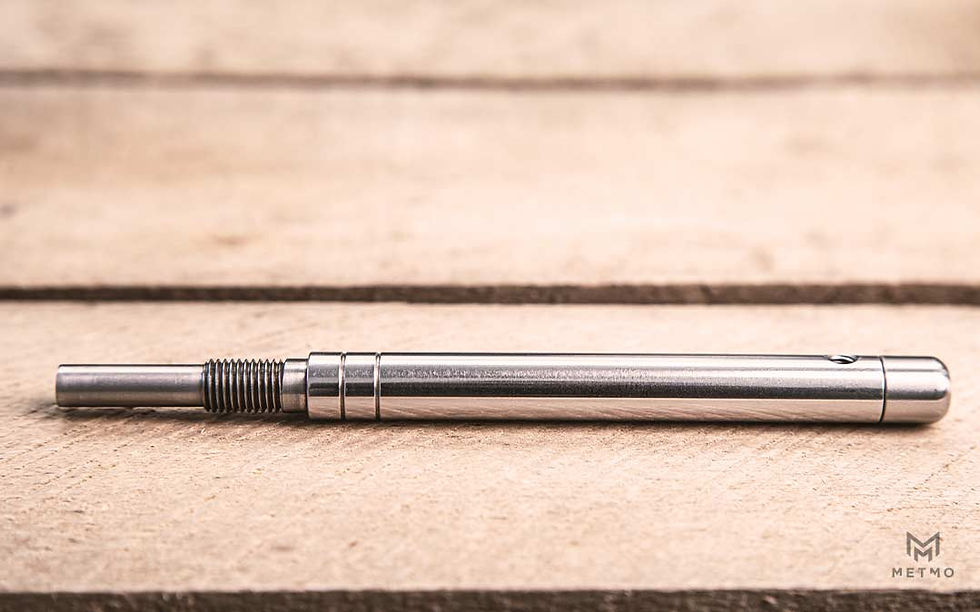
Handle
The largest part of Multi Drive, the handle. This is actually hollowed out from both ends, but the top end is sealed again by the bearing and end cap. This allowed us to reduce the weight gradually up the handle so that the balance is perfect when it's being used as a pencil, knife or scribe.
Other than the weight at the business end, where the chuck and collet connect, we unified a number of smaller parts that were on our earlier designs to make a much more rigid unibody that the collet connects into. The hexagon is precision EDM (electro discharge machining) cut into the end of the shaft with a second cone much like on the chuck that precisely closes the collet so that it holds items placed in it directly and exactly in the centre of the Multi Drive. Unesecerry... some might say... but why shouldnāt a pencil operate to the same level of precision as a CNC milling machine?Ā
This type of machining uses electrodes to basically vaporise metal to crazy tolerances! If you'd like to learn more about this type of machining, Steve Mould did an excellent overview of how wire EDM works (same principle as traditional EDM, but with really thin wire instead of big electrodes) using our MetMo Cube as an example.

Nubbin
This is a simple and mostly overlooked part of the design. Hiding away at the top of Multi Drive. This M4 grub screw was placed here so that it could be backed out a little bit to stop the round driver rolling away, or can be swapped for a dome head screw for a permanent anchor.Ā
This fixing point is also the perfect spot to attach a 3d printed clip, so the Multi Drive can be clipped to a pocket, if you are feeling adventurous!

Cap
The fiddle zone. Although fun to fiddle with, itās not just for entertainment. The cap provides a vital service for one handed use, letting pressure be applied to a screw while turningĀ with precision, really handy on a 0.2mm hex drive bit! It's also the only part that we couldnāt apply any weight reduction to due to it also having to be a spindle for a bearing, so itās still a solid billet. Fortunately, it's small enough so it's not adding a noticeable amount of weight. But on the bright side if you're an end of the pen chomper or a hungry alligator, the end cap can take your nibbling all day long.

Bearing
This is a stainless steel single row deep groove ball bearing, with seals on both sides, and according to the manufacturer āthey have low friction and are optimised for low noise and low vibration, which enables extremely high rotational speeds.ā Sounds like total overkill for a cap bearing on a screwdriver, so it was perfect for us!
In real terms though, because the area where it goes is so small even the best of bearings start to struggle with being pushed, pulled and chewed on by alligators. So, we had to go for something that would withstand that. We put the biggest bearings we could fit in here and made sure it was sealed so you wouldnāt have to worry about maintenance on them.
Watch out though, they are only rated to 130,000 rpm so donāt go trying to attach them to your turbine engines.
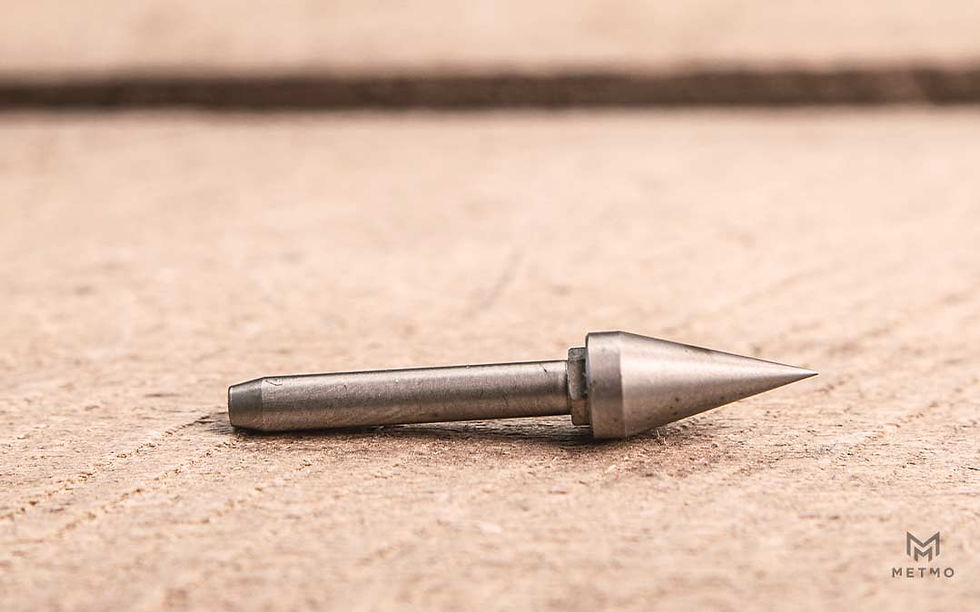
Scribe Adaptor
Scribe time. Some scribes are made of tungsten carbide but we have real trouble machining that, so these are hardened tool steel. Tool steel for reference is what you use to make cutting tools out of and what we use in our lathe to cut metal and make things like Multi Drivers. So, we figured it would be more than strong enough for marking up anything with daily use.
With a lot of use on metals like stainless steel and hardened metal they do wear down, but can easily be re-sharpened with a whetstone, or on a grinding wheel.
The holding end of the tip is the hidden part of the iceberg. With both a hexagon to engage and lock in and then the round spindle to add flexing stability, the combination of the two of these when put in the collet, turns the tip into a rigid part of the handle, so there is zero movement. Something we were aiming for to make this ultra precise to use.
And sure, you can break a toughened window with it, but itās a bit like using a Saturn 5 to open a bottle.Ā

4mm Drive Adaptor
A simple little adaptor that makes using multiple drive bits so much easier, itās not totally essential to use it with multi drive as the bits can be loaded directly into the collet if you were in a bind.
A press fit neodymium magnet in the base and the same locking mechanism as the scribe, make it nice and stable with some added reach and the convenience of quickly changing between the bits Ā

Blade Mount
This is the oldest part of the design and the only bit that has stayed the same since we first started this project. From the beginning we wanted a scalpel blade holder that was compatible with standard scalpel blades. With years of using various knives for modelling, we knew this would be the best way to go.
It turns out, everyone else who makes handles for these has them cast, and this is why in the past I have snapped handles due to cheap cast metals. We didnāt want to do that, so these are machined from a solid stainless-steel billet.
This was more challenging to machine the fine details and we do break a lot of cutters in the process of making these, so itās one of the slowest parts to make, but the end result is totally worth it and means it's strong, stable and has no flaws in the metal.Ā We have held short of hardening them so they can flex slightly on a microscopic level (sometimes flex is good!) increasing the long-term durability in use and after all, they're not being used as a hammer attachment... we hope.
Thatās a wrap!Ā
You are now a Multi Drive expert. If you ever need to operate on one, you can now do so safely. I hope you have enjoyed the deep dive in the what and why of the parts, but if you have any requests for other parts I have missed out beyond the core set, please let me know, I would be happy to expand! Ā
The Feedback Loop
We are still working away at a case that can hold everything and itās coming soon! But as a forewarning, she is a beast! We've also had some great feedback from various conversations on both KS and reddit and have put together a couple of extra attachments based on those ideas. We're planning to release them before the campaign ends for you all as some optional extras. A couple of them are quite niche, but I hope they can bring some joy to you all soon.
We have also been working on some free DIY print at home STL models, like this grip enhancer handle, or the āGripsterā as itās known internally. This has been requested by a few backers and internet snoopers and will be available at the end of the campaign to download. More on this design soon too! Ā Ā

That's all fine and good, but the chuck never engages the collet on my multi drive or my stubster, and you don't reply to emails.